Sikafloor®-400 N Elastic
Sikafloor®-400 N Elastic is a one part, highly elastic, solvent containing, moisture curing polyurethane resin coating.
- Easy-to-use 1-part technology
- Good resistance to abrasion (under normal pedestrian use)
- Very good crack-bridging ability
- Good mechanical resistance
- High elasticity
- Good resistance to UV exposure
- Good protection and weather resistance
- Semi-gloss finish
- Impermeable to liquids
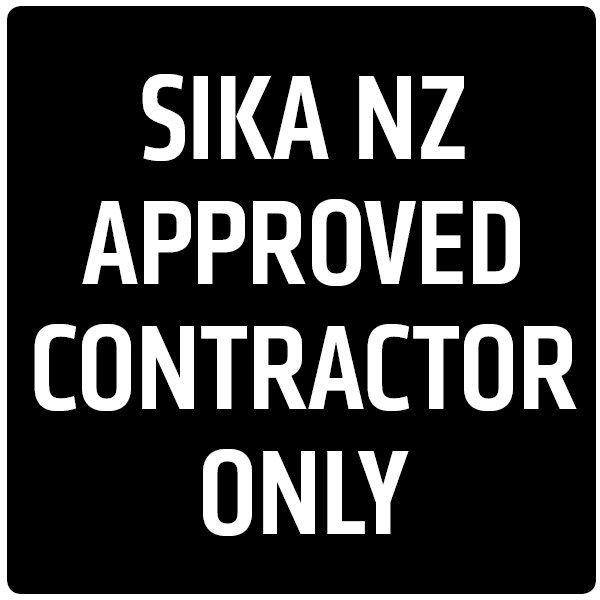
Usage
The Product is used as a:- Smooth and slip resistant coating on concrete and cementitious screed substrates
- Concrete
- Cementitious screeds
- The Product may only be used by experienced professionals.
- The Product may only be used for exterior applications.
Advantages
- Easy-to-use 1-part technology
- Good resistance to abrasion (under normal pedestrian use)
- Very good crack-bridging ability
- Good mechanical resistance
- High elasticity
- Good resistance to UV exposure
- Good protection and weather resistance
- Semi-gloss finish
- Impermeable to liquids
Packaging
18 kg
Colour
Appearance and colour | Coloured liquid |
Cured colour | A range of colour shades available - contact your Sika Rep for details |
Product Details
APPROVALS / STANDARDS
CE marking and declaration of performance based on EN 13813:2002 Screed material and floor screeds — Screed material — Properties and requirements — Synthetic resin screed material
CE marking and declaration of performance based on EN 1504-2:2004 Products and systems for the protection and repair of concrete structures — Surface protection systems for concrete — Coating
Chemical Base
Polyurethane
Shelf Life
6 months from date of production
Storage Conditions
The Product must be stored in original, unopened and undamaged sealed packaging in dry conditions at temperatures between +5 °C and +25 °C. Always refer to packaging.
Refer to the current Safety Data Sheet for information on safe handling and storage.
Density
~ 1.6 kg/l | (EN ISO 2811-1) |
Solid content by weight
~ 88 % | (EN ISO 3251) |
Solid content by volume
~ 77 % | (EN ISO 3251) |
Abrasion Resistance
Cured 7 days at +23 °C | 30 mg (CS 10 / 1000 / 1000) |
Chemical Resistance
Resistant to many chemicals. Contact Sika technical service. Wine, coffee, some leaves and flower petals and similar materials may cause surface discolouration. This will have no effect on the product performance and durability.
Service Temperature
Short term, maximum 8 hours | +100 °C |
Short term, maximum 7 days | +80 °C |
Permanent | +50 °C |
Application
Layer Thickness
Refer to the relevant System Data Sheet
Product Temperature
Minimum | +10 °C |
Maximum | +30 °C |
Ambient Air Temperature
Minimum | +10 °C |
Maximum | +30 °C |
Relative Air Humidity
Maximum | 80 % |
Minimum | 35 % or 45 % at > + 20 °C |
Dew Point
Beware of condensation. The substrate and uncured applied product must be at least +3 °C above dew point to reduce the risk of condensation on the surface of the applied product.
Substrate Temperature
Minimum | +10 °C |
Maximum | +30 °C |
Substrate Moisture Content
Substrate | Test method | Moisture content |
Cementitious substrates | Sika® Tramex moisture metre | ≤ 6 % |
Cementitious substrates | Calcium carbide method (CM-method) | ≤ 4 % |
No rising moisture according to ASTM (Polyethylene-sheet).
Osmosis caused by rising moisture or incorrect primer application is not covered by the product waranty.
Pot Life
The material in opened containers should be applied immediately. As soon as the container is opened, surface film formation will happen within 1–2 hours. High temperatures and high air humidity will accelerate curing significantly.
Waiting Time / Overcoating
Before overcoating the Product, allow:
Substrate temperature | Minimum | Maximum |
+10 °C | ~36 hours | ~5 days |
+20 °C | ~24 hours | ~3 days |
+30 °C | ~16 hours | ~2 days |
Note: Times are approximate and will be affected by changing ambient conditions, particularly temperature and relative humidity. Times are also dependant on layer thickness.
Applied Product Ready for Use
Temperature (50 % r.h.) | Rain resistant | Foot traffic | Full cure |
+10 °C | ~15 hours | ~24–48 hours | ~7–14 days |
+20 °C | ~5 hours | ~6–24 hours | ~5–9 days |
+30 °C | ~3 hours | ~4–18 hours | ~3–5 days |
Note: Times are approximate and will be affected by changing ambient conditions, particularly temperature and relative humidity. Times are also dependant on layer thickness.
Consumption
Type of application | Product | Consumption |
Light coating | Sikafloor®-400 N Elastic + (optional) 10 % by weight Sika® Thinner C | 0.4-0.6 kg/m² |
Sikafloor®-400 N Elastic Topcoat | 1.0-1.2 kg/m² | |
Medium Duty Coating | Primer 1-2 coats Sikafloor 150/151 | 0.4-0.6 kg/m² |
Sikafloor®-400 N Elastic Topcoat | 0.9–1.5 kg/m² | |
Heavy Duty Coating | Primer 1-2 coats Sikafloor 150/151 | 0.4-0.6 kg/m² |
Sikafloor®-400 N Elastic Basecoat | 0.8 kg/m² | |
Broadcast to refusal with Sika® Aggregate-501 | 4-6. kg/m² | |
Sikafloor®-400 N Elastic Topcoat | 0.5-1.1 kg/m² | |
On inclined areas with a gradient of up to 4 % | Sikafloor®-400 N Elastic | ~1 kg/m² |
Vertical and inclined areas with a gradient of ≥ 4 % | Sikafloor®-400 N Elastic + 1.5–2 % Sika® Extender T | 1.0–1.5 kg/m² |
Note: Consumption data is theoretical and does not allow for any additional material due to surface porosity, surface profile, variations in level, wastage or any other variations. Apply product to a test area to calculate the exact consumption for the specific substrate conditions and proposed application equipment.
APPLICATION INSTRUCTIONS
IMPORTANT
Strictly follow installation and maintenance procedures
Strictly follow installation and maintenance procedures as defined in Method Statements, application manuals and working instructions which must always be adjusted to the actual site conditions.
EQUIPMENT
APPLICATION EQUIPMENT
Smoothing trowel
Medium pile nylon roller
Brush
Squeegee
MIXING EQUIPMENT
Electric single paddle mixer (300 to 400 rpm)
SUBSTRATE QUALITY
Cementitious substrates (concrete / screed) must be structurally sound and of sufficient compressive strength (minimum 25 MPa) with a minimum tensile strength of 1.5 MPa
Substrates must be clean, dry and free of all contaminants such as dirt, oil, grease, coatings, laitance, surface treatments and loose friable material.
TREATMENT OF JOINTS AND CRACKS
Construction joints and existing static surface cracks in substrate require pre-treating before full layer application.
SUBSTRATE PREPARATION
TREATMENT OF JOINTS AND CRACKS
Except for stable, non-movement and shrinkage cracks – all cracks and junctions 1.0 mm and over are to be routed or saw cut and filled with Sikaflex-123 MS Bond polyurethane sealant to help accommodate minor structural movement (Refer to movement and elongation characteristics in the relevant Sika data sheets). The Sikaflex-123 MS Bond must be left to fully cure prior to the application of the Sikafloor-400 N Elastic
PREPARATION OF MINERAL SUBSTRATES
Rough and uneven surfaces must be levelled. Alternatively apply a scratch coat of Sikafloor®-150/-151, see individual product data sheets for further information.
PREPARATION OF TILED SUBSTRATES
Apply Sikafloor®-81 EpoCem or remove the glaze by sandblasting.
MIXING
Note: Add any additional required products before you start mixing.
- Before application, mix for at least 2 minutes or until the liquid and all the coloured pigment have achieved a uniform colour.
APPLICATION
IMPORTANT
No application on rising moisture
Do not apply on substrates with rising moisture.
IMPORTANT
Protect from moisture
After application, protect the Product from damp, condensation and direct water contact for at least 24 hours.
IMPORTANT
Temporary heating
If temporary heating is required, do not use gas, oil, paraffin or other fossil fuel heaters. These produce large quantities of both carbon dioxide and water vapour, which may adversely affect the finish.
- For heating, use only electric powered warm air blower systems.
IMPORTANT
Pin holes
If the Product is applied on porous substrates during rising temperatures, pin holes may form from rising air.
- Apply the Product during falling temperatures.
IMPORTANT
Ensuring consistent colour matching
For consistent colour matching, make sure the Product in each area is applied from the same control batch numbers.
IMPORTANT
Incomplete curing due to excessive thickness
If the product is applied at an excessive thickness, it may not cure properly.
- Make sure to follow the consumption as specified in the Application Information.
PRIMER
- Pour the Product onto the surface.
- Apply the Product evenly over the surface with a brush, fleece roller or a squeegee.
- Back roll the surface in two directions at right angles with a fleece roller.
SMOOTH COATING
- Pour the Product onto the surface.
- Apply the Product evenly over the surface with a medium pile roller.
SLIP-RESISTANT BROADCAST LAYER
- Pour the mixed Product onto the prepared substrate.
- Apply the Product evenly over the surface with a trowel.
- Back roll the surface in two directions at right angles with a spike roller.
- Allow the product to cure for 15 minutes.
Note: Times are temperature dependant. Times given are for +20 °C. - Broadcast the surface with quartz sand or silicon carbide, lightly at first, then to excess.
Note: The aggregate is dependant on the system build-up. Refer to the relevant System Data Sheet. - Allow the surface to become tack free.
- Remove all loose sand with industrial vacuuming equipment.
CLEANING OF TOOLS
Clean all tools and application equipment with Sika® Thinner C immediately after use. Hardened material can only be removed mechanically.