Sikagard®-62
Sikagard®-62 is a two part, rigid, 100 % solids, coloured high build epoxy resin based protective coating.
- Solvent free
- Good mechanical and chemical resistance
- High build
- Impervious to liquids
- Easy to mix and to apply
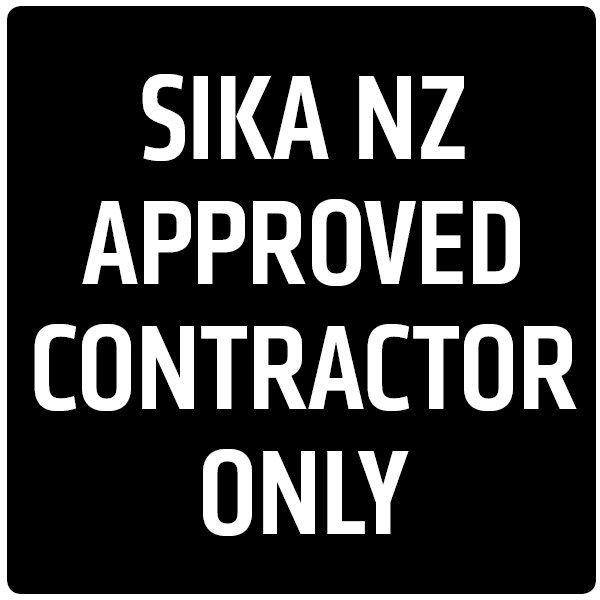
Usage
- Chemical resistant protective layer on concrete, stone, cementitious mortars and renderings, epoxy cement, epoxy resin based products and steel
- Lining in storage tanks and silos
- Anti-corrosion coating on steel in food processing plants, sewage works, farms, agricultural enterprises, chemical and pharmaceutical facilities and beverage industry
Advantages
- Solvent free
- Good mechanical and chemical resistance
- High build
- Impervious to liquids
- Easy to mix and to apply
Packaging
Part A (including pigment pack) | 9 kg |
Part B | 3 kg |
Total Kit (A+B) | 12 kg |
Colour
A limited range of other RAL colours are available
Product Details
ENVIRONMENTAL INFORMATION
Conformity with LEED v2009 IEQc 4.2: Low-Emitting Materials - Paints and Coatings
APPROVALS / STANDARDS
- AS/NZ 4020:2005 Compliance Testing for Potable Water
- Coating for concrete protection according the requirements of EN 1504-2:2004, Declaration of Performance 0206060100100000011008, certified by FPC Notified Body and provided with CE marking
- WRAS, test report No. M104991, 2011, Contact with water for wholesome purposes according BS 6920-1:2000
Chemical Base
Epoxy resin
Shelf Life
Part A: Twenty-four (24) months
Part B: Twenty-four (24) months
From date of production if stored properly.
Storage Conditions
The packaging must be stored properly in original, unopened and undamaged sealed packaging, in dry conditions at temperatures between +5 °C and +30 °C. Protected from direct sunlight.
Density
Part A | ~1.45 kg/l |
Part B | ~1.02 kg/l |
Mixed resin ~1.37 kg/l
Density values determined at +23 °C
Shore D Hardness
~80 | (DIN 5305) |
Mechanical Resistance
Taber Abraser | CS 10/ 1000/ 1000 | 24.4mg |
Taber Abraser | CS 17/ 1000/ 1000 | 70 mg |
Taber Abraser | H 22/ 1000/ 1000 | 560.6mg |
Tensile Adhesion Strength
> 1.5 MPa to concrete | (ISO 4624) |
Thermal Resistance
Exposure | Dry heat |
Permanent | +50 °C |
max. 7 days | +80 °C |
max. 12 hours | +100 °C |
Chemical Resistance
Please contact Sika technical service for specific information.
Application
Mixing Ratio
Part A : Part B = 3 : 1 by weight
Layer Thickness
~0.2 mm per layer
Ambient Air Temperature
+8 °C min. / +30 °C max.
Relative Air Humidity
< 80 %
Substrate Temperature
+8 °C min. / +30 °C max.
Minimum 3 °C above dew point, beware of condensation
Pot Life
Temperature | Time |
+10 °C | ~30 min |
+20 °C | ~20 min |
+30 °C | ~10 min |
Waiting Time / Overcoating
Temperature | Min. | Max. | Full cure |
+10 °C | ~ 30 hours | ~ 3 days | ~ 14 days |
+20 °C | ~ 10 hours | ~ 2 days | ~ 10days |
+30 °C | ~ 6 hours | ~ 1 day | ~ 5 days |
Consumption
~0.30 kg/m² per layer
APPLICATION INSTRUCTIONS
SUBSTRATE QUALITY
The substrate must be sound, clean, dry, free from contaminants such as dirt, grease, oil, old coatings, release agents, laitance and other adhesion preventing or influencing substances.
On high absorbent, non-sound, contaminated, not cement based substrates precautions have to be taken and a suitable primer has to be used.
SUBSTRATE PREPARATION
Concrete Substrate
Concrete substrate must be prepared mechanically to achieve an open textured surface.
Weak areas in the substrate must be removed and surface defects such as blowholes and voids must be fully exposed.
All dust, loose and friable material must be completely removed from all surfaces before application of the product, preferably by brush and/or vacuum.
Open voids and blowholes need to be closed with a suitable Sika® pore filling mortar. The roughness of the substrate needs to be levelled with a suitable Sika® rendering and levelling mortar.
Steel Surface
Steel surface must be prepared mechanically using abrasive blast cleaning. The level SSPC-SP 10 “near white metal blast cleaned” or level Sa 2.5 according to ISO EN 12944-4 has to be achieved. Welds and joints have to be prepared according to EN 14879, part 1. After blast cleaning remove all dust dirt and blasting material. In order to maintain the surface conditions after blast cleaning air-conditioning is recommended.
MIXING
Prior to mixing stir part A mechanically. When all of part B has been added to part A mix continuously for 3 minutes until a uniform mix has been achieved. Use a low speed electrical stirrer (300–400 rpm) to avoid air entrapment. To ensure proper mixing pour material into a clean container and stir again.
APPLICATION
Apply by brush, roller or airless spray.
CLEANING OF TOOLS
Clean all tools with Sika® Thinner C immediately after use. Hardened and/or cured material can only be removed mechanically.