Sikaflex® AT Facade
Sikaflex® AT Facade is a 1-part, STP, moisture-curing, elastic sealant.
- Low modulus
- Very good workability
- Over-paintable*
- Highly resistant to weathering
- Movement capability ± 25% (ISO 9047)
- Low stress on substrates
- Very low VOC emissions
- Primerless for most substrates and applications
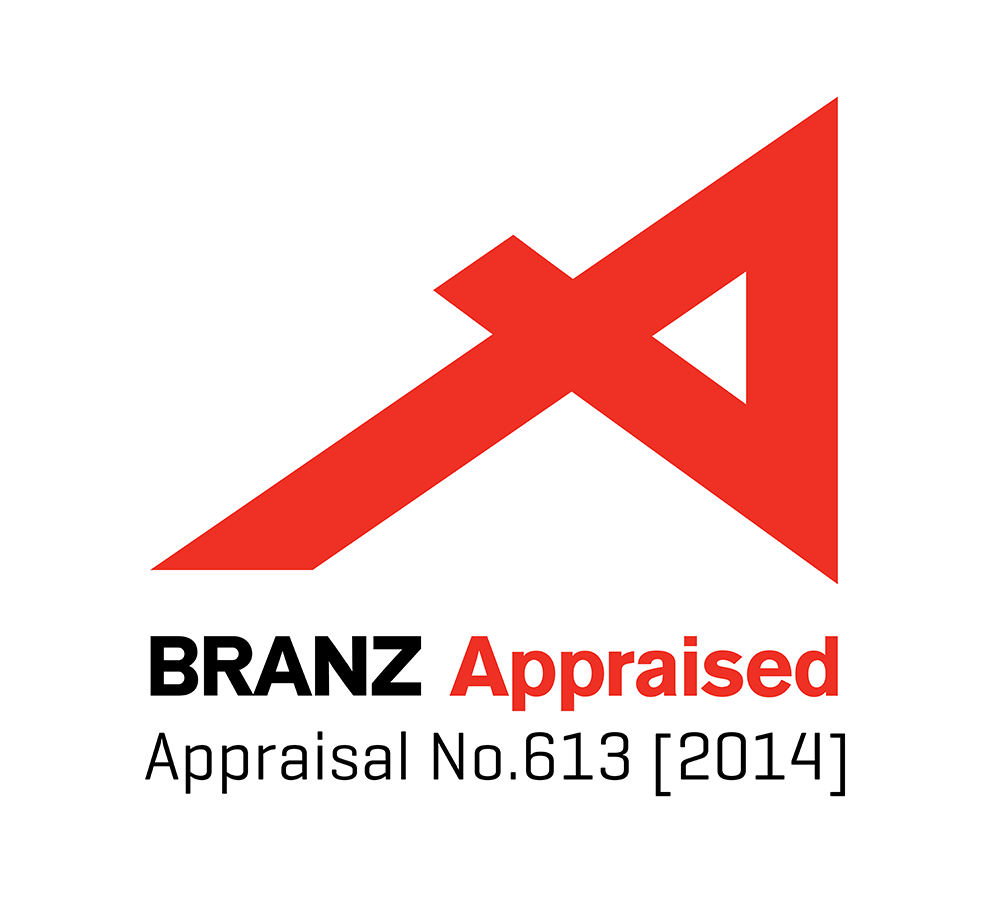
Usage
Sikaflex® AT Facade is designed for joint sealing ofmovement and connection joints, porous and non-porous
substrates such as concrete, brick, steel metals. Sealing joints for:
- Facade elements
- Movement and connections
- Infill panels
- Cladding
- Curtain walling
- Interior and exterior use
Advantages
- Low modulus
- Very good workability
- Over-paintable*
- Highly resistant to weathering
- Movement capability ± 25% (ISO 9047)
- Low stress on substrates
- Very low VOC emissions
- Primerless for most substrates and applications
Packaging
300 ml cartridge | 12 cartridges per box |
600 ml foil pack | 20 foil packs per box |
Colour
White, Grey, Black
Product Details
ENVIRONMENTAL INFORMATION
- VOC emission classification GEV-Emicode EC1PLUS, license number 3865/20.10.00
- LEED v4 EQc 2. Low-Emitting Materials
APPROVALS / STANDARDS
-
CE Marking and Declaration of Performance to EN 15651-1 - Sealants for non-structural use in joints in buildings - Facade elements - F-EXT-INT CC
-
ISO 11600-F Class 25LM, Sikaflex AT-Facade, SKZ, Report, No 102993/12-II
-
DIN 18540-F, Sikaflex AT-Facade, SKZ, Report, No 70268/2
-
BRANZ Appraised, Appraisal No.613 (2024)
NZ Building Code Compliant
- B2 Durability: Clauses B2.3.1 (b) 15 years. (c) 5 years
- E2 External Moisture: Clause E2.3.2
- F2 Hazardous Building Materials: Clause F2.3.1
Chemical Base
Silane terminated polymer (STP)
Shelf Life
12 months from date of production
Storage Conditions
The product must be stored in original, unopened and undamaged packaging in dry conditions at temperatures between +5 °C and +25 °C.
Always refer to packaging.
Density
~1.30 kg/l | (ISO 1183-1) |
Product Declaration
EN 15651-1 F EXT-INT CC
DIN 18540-F
ISO 11600 F 25 LM
Compatibility
Compatible with the following substrates:
Non-porous substrates
Aluminium, anodised aluminium, stainless steel, copper, brass, titanium-zinc, PVC, galvanised steel, powder coated metals, glazed tiles
Porous substrates
Concrete, aerated concrete, brick, cement based renders and mortars
For other types of substrates contact Sika Technical Services for additional information
Shore A Hardness
~25 (after 28 days) | (ISO 868) |
Secant Tensile Modulus
~0.30 N/mm2 at 100 % elongation (+23 °C) | (ISO 8339) |
~0.50 N/mm2 at 100 % elongation (−20 °C) |
Elastic Recovery
~95 % | (ISO 7389) |
Tear Propagation Resistance
~5.5 N/mm | (ISO 34) |
Movement Capability
± 25 % | (ISO 9047) |
Resistance to Weathering
10 | (ISO / DIS 19862) |
Service Temperature
-40 °C to +90 °C
Joint Design
The joint dimensions must be designed to suit the movement capability of the sealant. The joint width must be a minimum of 6 mm and a maximum of 50 mm. A width to depth ratio of 2:1 must be maintained. Joint widths less than 10 mm are generally for interior connection joints or crack control joints and therefore considered as non-movement joints.
Example of typical joint widths for joints between concrete elements for exterior applications if the joint sealant is classified as ±25 % movement capability according to ISO 9047, calculation according to DIN 18540:
Joint distance in m | Min. joint width in mm | Min. joint depth in mm |
2 | 10 | 10 |
4 | 15 | 10 |
6 | 20 | 10 |
8 | 30 | 15 |
10 | 35 | 17 |
All joints must be correctly designed and dimensioned in accordance with the relevant standards and codes of practice before their construction. The basis for calculation of the necessary joint widths are:
- The type of structure
- Dimensions
- Technical values of the adjacent building materials
- Joint sealing material
- The specific exposure of the building and the joints
For joint design and calculations contact Sika® Technical Services for additional information.
Application
Backing Material
Use closed cell, polyethylene foam backing rod
Sag Flow
0 mm (20 mm profile, +50 °C) | (ISO 7390) |
Ambient Air Temperature
+5 °C to +40 °C
Substrate Temperature
+5 °C to +40 °C. Minimum +3 °C above dew point temperature
Curing Rate
~3 mm/24 hours (+23 °C / 50 % r.h.) | (CQP* 049-2) * Sika Corporate Quality Procedure |
Skin Time
~80 minutes (+23 °C / 50 % r.h.) | (CQP 019-1) |
Tooling Time
~65 minutes (+23 °C / 50 % r.h.) | (CQP 019-2) |
Consumption
Joint width [mm] | Joint depth [mm] | Joint length [m] per 600 ml foil pack |
10 | 10 | 6 |
15 | 10 | 4 |
20 | 10 | 3 |
25 | 12 | 2 |
30 | 15 | 1.3 |
These figures are theoretical and do not allow for any additional material due to surface porosity, surface profile, variations in level or wastage etc.
SUBSTRATE PREPARATION
The substrate must be clean, dry, sound and free from oils, grease, dust, cement laitance and loose or friable particles.
The substrate must be sound, clean, dry and free of all contaminants such as dirt, oil, grease, cement laitance, old sealants and poorly bonded paint coatings which could affect adhesion of the sealant. The substrate must be of sufficient strength to resist the stresses induced by the sealant during movement.
Removal techniques such as wire brushing, grinding, grit blasting or other similar mechanical tools can be used.
Repair all damaged joint edges with suitable Sika repair products.
Sikaflex® AT Facade adheres without primers and/or activators.
For optimum adhesion, joint durability and critical, high performance applications such as joints on multi-storey buildings, highly stressed joints, extreme weather exposure or water immersion / exposure. The following priming and/or pre-treatment procedures must be followed:
Non-porous substrates
Aluminium, anodised aluminium, stainless steel, PVC, galvanised steel, powder coated metals or glazed tiles. Lightly roughen surface with a fine abrasive pad. Clean and pre-treat using Sika® Aktivator-205 applied with a clean cloth.
Before sealing, allow a waiting time of > 15 minutes (< 6 hours).
Other metals, such as copper, brass and titanium-zinc, clean and pre-treat using Sika® Aktivator-205 applied with a clean cloth. After a waiting time of > 15 minutes (< 6 hours). PVC has to be cleaned and pre-treated using Sika® Primer-215 applied with a brush. Before sealing, allow a waiting time of > 30 minutes (< 8 hours).
Porous substrates
Porous substrates
Concrete, aerated concrete and cement based renders, mortars and bricks surfaces must be primed using Sika® Primer-3 N applied by brush.
Before sealing, allow a waiting time of > 30 minutes (< 8 hours).
Adhesion tests on project specific substrates must be performed and procedures agreed with all parties before full project application.
Note: Primers and activators are adhesion promoters and not an alternative to improve poor preparation / cleaning of the joint surface. Primers also improve the long term adhesion performance of the sealed joint.
Contact Sika Technical Services for additional information.
MIXING
1-part ready to use
CLEANING OF TOOLS
Clean all tools and application equipment with Sika® Remover-208 immediately after use. Hardened material can only be removed mechanically.
For cleaning skin use Sika® Cleaning Wipes-100.